KTEG ZE150W
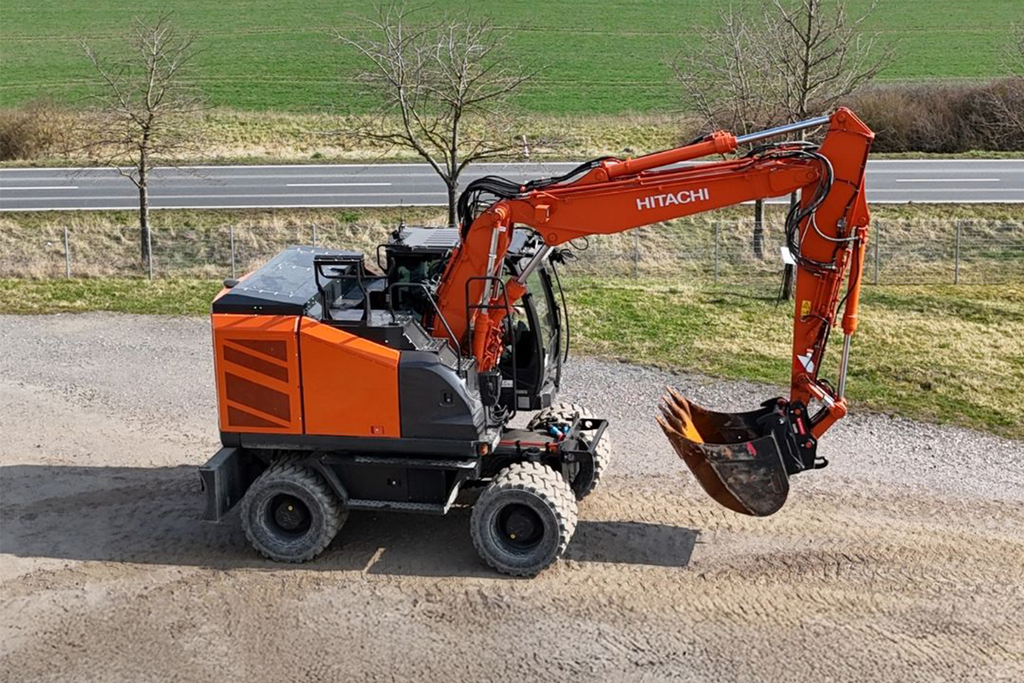
Introduction and objectives
In this innovation-oriented project, SUNCAR worked with KTEG on the development and market testing of a battery-powered wheeled excavator in the 15-ton class. These machines are preferably used for inner-city construction sites, as they are permitted to drive on public roads with the appropriate license.
The aim of the project was to optimize the efficiency of the wheeled excavator electrically through a radically revised drive concept and to create a resource-saving and environmentally friendly alternative to diesel-powered machines. The locally emission-free operation and significant noise reduction are key advantages that make urban use particularly attractive. Electrification also has a positive effect on the user experience, as undivided power is always available for every movement. The reduced energy requirement is also reflected in even lower operating costs and reduced maintenance costs compared to diesel excavators.
Procedure and technological approaches
As part of the project, SUNCAR and KTEG developed two prototypes with different electrical expansion stages. This allowed different drive concepts to be compared with each other: a fully hydraulic, electrohydraulic and quasi-fully electric system. A key part of the optimization was to improve the drive concept in order to use the energy used more efficiently and to enable it to be fed back into hydraulic and electrical storage systems. This brings with it a variety of new challenges, particularly because the remaining hydraulics should continue to function as usual.
Special attention was also paid to the battery technology. The choice of battery not only influences the range and performance of the excavator, but also the charging times and the overall service life of the system. Various battery types and their possible applications were therefore analyzed.
Challenges and solutions
One of the biggest challenges was the limited availability of electrical and mechanical components. Long delivery times and less mature product lines led to a complex selection process. In addition, some of the hydraulic routing had to be completely redesigned in order to integrate the new systems without taking up unnecessary space. The temperature management of the battery was also optimized, as the efficiency of the battery cells depends heavily on the operating conditions. Targeted cooling and an improved energy management system were implemented to maximize battery life and ensure consistent performance.
Despite the many new aspects of the project and the associated challenges, it was ultimately possible to develop a component architecture that enables a full working day with just one battery charge. This represents a significant advantage over previous electric excavators, which often have shorter operating times. Thanks to the modular design of the battery unit, the system can be adapted to different operating conditions, which ensures a high degree of flexibility in construction site operations.
Results and conclusions
The tests of the prototypes have so far shown a significant reduction in energy consumption. In particular, the configuration with the direct electric drive achieved a saving of around 40 percent compared to a purely electro-hydraulic variant. In addition to energy savings, noise measurements were also carried out to further investigate the advantages of electric drive technology in urban construction sites. The results showed a significant reduction in noise pollution, which is a decisive advantage, especially in densely populated areas.
Practical tests were also carried out with different driving modes in order to find the optimum balance between performance and energy efficiency. The data collected was incorporated into the further development of the control algorithms in order to further minimize energy consumption and maximize operational safety. Charging cycles and integration into existing charging infrastructures were also of particular importance. It was evaluated how fast-charging systems and exchangeable batteries could further improve operation.
In conclusion, battery electric wheeled excavators represent a promising solution for the sustainable construction sector. The combination of high energy efficiency, reduced emissions and improved working comfort makes them an innovative and economical alternative for urban construction site operations. In the long term, demand for such machines is expected to increase as more and more cities demand emission-free construction sites. The knowledge gained from this project forms a solid basis for the further development and series production of this new generation of wheeled excavators.
More about the KTEG electric excavators: